

It provides a high degree of chemical resistance against petroleum-based gasoline, diesel, and ethanol fuel blends.
Corrosion Of Aluminum Fuel Tanks From Ethanol Blended Fuels
MAX GRE forms a protective barrier that prevents corrosion of aluminum fuel tanks, largely used in boats and commercial vehicles, from ethanol fuel blends (E10, E15, E85 Gasoline Or Diesel).
To learn more about alcoholate corrosion of aluminum, please perform a web search on "Ethanol Aluminum Tank Corrosion.
Surface Preparation Prior To Application
The efficacy of any product used for similar applications is dependent on how well the surface is prepared to ensure a strong bond.
For repairing or coating used or old tanks, the substrate requires degreasing to remove lubricants and fuel additive residue.
This critical step applies to both metal and composite tanks.
The strength of adhesion is dependent on how well the substrate is prepared.
Please review the following video demonstration.
The video demonstrates how the surface tension of a solid surface affects the wettability of the applied liquid.
The liquid can be an adhesive coating, colored paints, or printing inks.
Good substrate wetting yields good adhesion, may it be for coating applications, composites fabrication, or general bonding use.
The substrate, metal or otherwise must be cleaned appropriately to remove oily residue by chemical degreasing.
Use acetone to degrease the surface and ensure that the substrate is dry and free from contamination before application.
Do not use rubbing alcohol or denature alcohol; acetone works best for degreasing and removing surface residue that affects adhesion.
Remove loose or flaking rust, and for the best adhesion performance, abrade or sandblast the surface to bare condition
so the MAX GRE A/B coating is in direct contact with the substrate.
For aluminum substrates, chromic acid etching is recommended for bonding and coating applications.
Use the same water bead test to determine the wettability of the substrate. If the water does not form a continuous film as demonstrated in the video
The Following Surface Preparation Procedures Are Recommended.
METALS AND CONCRETE Degrease Metals– Wipe surface with lint-free rag dampened with Methyl Ethyl Ketone (MEK) or acetone to remove all oil, dirt, and grease. Etch Metals – For optimum results, metal parts should be immersed in a chromic acid bath solution consisting of:
The solution is held at 160°F (71°C), and the parts left immersed for 5 to 7 minutes. Rinse – remove metal parts from etching bath and rinse with clean water. (distilled water is recommended). Etch Concrete- Use commercially sold concrete etching solution (hydrochloric acid based works best). Neutralized per instructions, rinse and allow to dry thoroughly. ALTERNATE PROCEDURE Degrease and dry – Degrease the surface as noted above, sand or sandblast the surface lightly but thoroughly. Rinse with acetone or Methyl Ethyl Ketone (MEK), and dry. | GLASS Degrease – With MEK as above, or with a strong boiling solution of a good grade household detergent. Etch – For optimum results, degreasing can be followed by the chromic acid bath outlined above. WOOD Sand – Bonding surfaces should be sanded lightly, but thoroughly to remove all external contamination. Clean – Carefully remove all dust, or particles of wood from sanded areas. A stiff and clean brush or compressed air can be used. PLASTIC Clean – Remove all dirt, oil, or other surfaces contaminated with detergent soap or degreasing solvent and water, followed by thorough rinsing and drying. A solvent that does not have a detrimental effect may also be used. Sand – Surfaces to be bonded should be sanded lightly, but thoroughly to remove surface sheen. Clean – Carefully remove all dust or particles of plastic from the sanded area. A clean brush, lint-free cloth, or compressed air may be used. |
Mixing And Application
Precaution: As with industrial chemicals of the same nature, avoid direct skin contact using protective gloves and eyewear. Ensure the work area is well ventilated and extinguish any flame source to prevent fuel vapors accidental ignition.
Always practice safety first.
The Use Of A Weighing Scale Is Highly Recommended For Measuring The Resin To Curing Agent Mix Ratio.
Purchase this scale with any of our offering &the shipping cost of the scale is free.
https://www.ebay.com/itm/222630300203
Shipping overpayments are refunded back after completion of sale.
MAX GRE A/B is mixed 2:1 by weight or by volume and offers a 35 to 45 minute working time.
Use a scale to measure the proper mix ratio accurately, which dramatically affects cured chemical resistance, especially when mixing small batch sizes.
The mixed consistency is similar to cooking oil.
MAX GRE is self-leveling and will continue to flow until the MAX GRE resin gels or converts to a solid.
The resin system used in the video demonstration is different than the MAX GRE.
The dynamics of exothermic heat release is applicable to any room-temperature cured epoxy resin.
Coatings: Apply The MAX GRE Using A Brush Or Roller Coat.
The ideal coating thickness for a chemical resistant barrier is 0.015-inch or 15 mils dry film thickness.
It may require several applications to achieve the target coating thickness.
Allow the first coat to cure for 5 to 6 hours at 75°F and repeat the application directly on top of the previous application.
Once the desired thickness is achieved, allow the MAX GRE to fully cure 36 to 48 hours at 25°C to 30°C before use.
To use the MAX GRE as an adhesive, prepare the substrates to their bare condition, so the MAX GRE is directly applied and in complete contact with the base substrate.
Ensure bond footprint is relative to the amount of force that is expected.
Mix the proper amount of the resin and curing agent for the application.
Apply the mixed MAX GRE on both substrates to be bonded and assemble.
Apply sufficient clamping force to ensure both substrates are mated until the MAX GRE cures.
Allow to cure for 12 to 18 hours at room temperature for the MAX GRE to be tack-free and handleable.
Allow the MAX GRE to cure for 36 to 48 hours at 25°C to 30°C before using fuels.
During the colder season, where the ambient temperature is below 70°F, MAX GRE requires a longer cure time.
Potting Compound: MAX GRE A/B Is Self Leveling And Suitable For Thick Potting Or Casting Application
MAX GRE also works well as a potting compound for encapsulating fuel level sensors.
It is suitable for up to a ¾-inch thick casting or embedding.
Upon cure, MAX GRE is non-conductive and provides electrical insulation for low voltage signals for gauges and meters.
MAX GRE bonds well to copper wires and holds connections in place.
It is resistant to pull-outs from expansion and contraction coefficients and mechanical vibration from average use and environment.
Impregnating Resin For Fiberglass Or Carbon Fiber
As an impregnating resin for composite fabrication, use silane or volan treated fabrics for the best epoxy resin compatibility and wet-out.
Saturate the fabric with the mixed MAX GRE at 33 percent resin content.
Allow to fully cure for 48 hours at 25°C to 30°C before use.
Observe composite fabricating guidelines for making fuel cells.
See COMPOSITE FABRICATING BASICS Below For More Details
MAX GRE Chemical Resistance Test
Cured MAX GRE Specimens in E85 Gasoline Continuous Immersion Test
Specimens have been in total immersion in E85 gasoline and diesel E85 fuel since 06/15/2009 with no change in its cured properties.
The stability in weight or hardness (Shore Durometer) of the MAX GRE demonstrates its superior chemical resistance to modern fuels.
No Change In Weight Or Durometer Hardness Demonstrating Its Chemical Resistance Properties.
Hardness Test After Continuous Immersion In Fuel
Testing the Shore Durometer Hardness of the specimens determines if the cures resin is being affected by the gasoline immersion.
The weights and Durometer Hardness of the specimens were measured before and after the immersion test.
Weight change greater than 1% is deemed unsuitable for chemical-resistant applications.
After several years of continuous gasoline immersion, the MAX GRE test specimens exhibit no weight or hardness changes.
Poor chemicals resistance will bloat the specimens, increasing in mass and reduce in Shore Durometer Hardness.
MAX GRE A/B has proven its excellent resistance against various petroleum fuels.
Testing For Weight Change, Durometer Hardness After Continuous Gasoline Immersion.
Negligible Change In Weight (Less Than 0.03%) Measured Demonstrating Excellent Gasoline And Diesel Resistance.
June 2009 | Start Date |
March 2014 | No appreciable change in dimension, weight, and Durometer Hardness |
February 2017 | No appreciable change in dimension, weight, and Durometer Hardness |
November 2019 | No appreciable change in dimension, weight, and Durometer Hardness |
November 2020 | No appreciable change in dimension, weight, and Durometer Hardness |
Coverage And Use Metrics
Coating Coverage
48 Ounce Kit Coverage At 0.030 Inch Coating Thickness = 20 Square Feet
Fiberglassing Application
48 Ounce Kit Coverage With 9 Ounce Per Square Yard Fiberglass Cloth
Using 70/30 Fabric To Resin Ratio By Weight
6.5 Square Yards Of 10 Ounce Fiberglass Per This 48 Fluid Ounce Kit.
7781 Style 8 Harness Satin Weave Available In Cut Lengths
Free Shipping For All Fiberglass Fabrics
2 Yards Continuous Length
By 60 Inches Wide
https://www.ebay.com/itm/223669319695
5 Yards Continuous Length
By 60 Inches Wide
https://www.ebay.com/itm/223508087559
10 Yards Continuous Length
By 60 Inches Wide
https://www.ebay.com/itm/313471251199

Click the link to view the description page and add to cart
2 Yards Continuous Length By 60 Inches Wide
https://www.ebay.com/itm/223669319695
5 Yards Continuous Length By 60 Inches Wide
https://www.ebay.com/itm/223508087559
https://www.ebay.com/itm/313471251199
This weave style is also much tighter and has less opening between the fiberglass yarn.
Once impregnated with the MAX GRE resin, the laminate is impermeable and provides hermetic sealing.
8-Harness Satin Weave Fiberglass Conformity To Curves And Contours
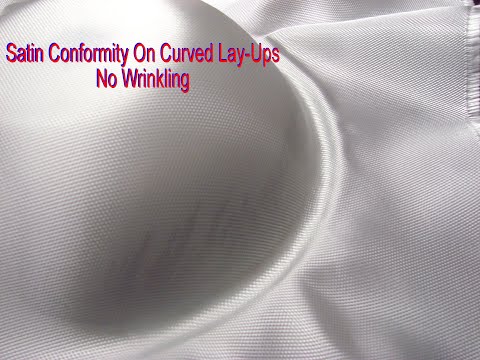
Fiberglass Fabric For Curved And Contours. 8 Harness Satin Weave For Less Wrinkling And Distortions
Video will open in a new window
Using the eBay App? Paste link into a browser window:
PHYSICAL AND MECHANICAL PROPERTIES OF MAX GRE A/B