96 OUNCE KIT
1/2 gallon of Resin
1 Quart of Curing Agent
3/4 Gallon Combined Volume
Low Viscosity (Thin Consistency), Easy To Use And Apply
Slow Setting To Allow More Time To Flow And Saturate Voids And Reinforce Damaged Wood Rot
EPS Foam Safe, MAX GPE A/B Will Not Dissolve Styrofoam Materials (XPS & EPS Type)
Practically Odor Free, 100% Solids Formulation, Non-Flammable
Cures Hard And Durable After 24 Hours Of Cure At 75°F
MAX GPE IS USED BY MANY OF OUR CUSTOMERS FOR:
MAX GPE A/B is a two-component epoxy based resin system designed to provide a broad range of mechanical and physical properties.
MAX GPE A/B Is suitable use for almost all types of epoxy resin applications.
It can be utilized as a structural adhesive demonstrating excellent adhesion to a wide selection of substrates.
Upon cure MAX GPE A/B is chemical resistant for protective coating, and sealing.
It works well as impregnating resin for fiberglassing applications, or as a waterproofing sealant for porous substrates
potting applications for electronics and as a casting resin for large and small applications.
Repair Videos For RV Panel Delamination
Click Play To View The Video
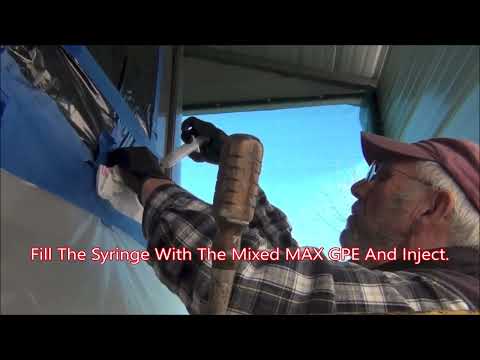
MAX GPE RV Panel Delamination Repair Glue
Video will open in a new window
Using the eBay App? Paste link into a browser window:
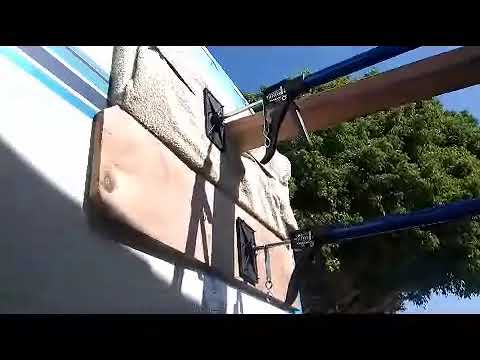
MAX GPE RV REPAIR CUSTOMER REVIEW
Video will open in a new window
Using the eBay App? Paste link into a browser window:
SAFE TO USE ON POLYSTYRENE FOAM
MAX GPE A/B Fiberglass Reinforced EPS And XPS Foam
Create A Rigid Fiberglass Shell To Reduce Impact Damage
Fiberglass Fabric Suitable For Foam Reinforcement:
Style 7781 8 Harness Satin Weave Fiberglass Fabric
Inquire For Combine Shipping
3 Yards Long By 60 Inches Wide: https://www.ebay.com/itm/223669319695
MAX GPE A/B is mixed two parts Resin to one part Curing Agent by weight or by volume (2:1).
The mixed consistency is low in viscosity, clear and easily poured, injected or brush applied into place.
MAX GPE A/B has a 60 minutes gel time that allows adequate working time for casting, coating, bonding and potting or encapsulating applications.
MAX GPE A/B performs well as an adhesive for metals, alloys, plastic, wood, stones & concrete, fiberglass and other substrates that require high tensile shear strength properties.
MAX GPE A/B is an excellent choice for composite fabrication using fiberglass, carbon fiber, Aramid, and other hybrid fabrics.
Its low viscosity allows fast fabric wet-out resulting in a minimal void and laminate porosity.
Cured composites fabricated with MAX GPE A/B exhibits exceptional mechanical properties such as impact resistance, compressive and tensile strength.
As a casting resin and potting compound, MAX GPE A/B cures non-electrically conductive and demonstrates good dimensional stability.
Pre-Mix And Mixing Notes
Prepare all needed tooling and materials before mixing the resin and curing agent together.
Determine the amount of resin and curing agent needed.
The batch size should be no more than you can apply within the 60-minute working time.
The working time may be shorter if the temperature is above 80°F and longer if the temperature is below 70°F.
Note that large batch size will react quicker or if the mixture is kept in a concentrated mass.
The exothermic heat that is released during the chemical reaction generates will cause the mixture to cure faster.
Pour the desired amount of resin then the curing agent (2:1 mix ratio) in a clean container and gently mix with a spatula or mixing blade until a uniform blend is achieved.
Scrape the sides and bottom of the container and mix until clear and uniform in consistency.
Transfer the mixture into another container and mix for another 2 minutes.
This technique ensures a homogenous blend and prevent tacky spots from occurring.
Please View The Mixing Demonstration Video Below.
Pour, inject or apply the resin directly onto the prepared surface and allow to cure for at least 24 to 36 hours.
The applied resin will set-up in 4 to 6 hours and can be handled after 12 hours at 75° F (25° C).
Allow the application to cure fully for 2 to 3 days before use.
Physical Properties
Viscosity |
900 cPs Mixed |
Mix Ratio |
100 parts A to 50 parts B by weight or volume |
Working Time |
65 Minutes at 200 Gram Mass |
Peak Exotherm |
160oC |
Time To Reach Peak |
80 Minutes |
Density |
1.10 g/cc Cured |
Cure Time |
1 to 3 days at 25oC |
Heat Cure |
2 Hours @ 25oC Plus 1 Hour @ 120oC |
Set-To-Dry @ 10 Mil Film |
6 Hours |
Surface Dry |
9 Hours |
Handling Time |
8 Hours |
Cured Mechanical Properties
(1) Test Specimens Were Cured 2 hours at 80°C plus 2 hours 110°C
Test Criteria | Room Temp Cure | Room Temp + Heat Cure |
Hardness | 78 D | 81 D |
Izod Impact ft-lb/in | .13 | .19 |
Tensile Shear Strength psi | 3,100 | 3,765 |
Tensile Strength psi | 9,600 | 12,300 |
Tensile Modulus psi | 460,000 | 489,120 |
Ultimate Elongation % | 3.8 | 2.3 |
Heat Distortion Temperature | 84°C | 110°C |
Compressive Strength | 12,300 | 13,000 |
24 Hours Water Boil % Weight Gain | 2.2 | 1.8 |
Heat Post Curing Technique For Faster Cure
Use An Infrared Heat Lamp For Larger Parts.



Epoxy Resin Mixing And Usage Applications
Please View The Following Video For The Proper Mixing Of Epoxy Resins.
It demonstrates the proper technique of mixing any type of epoxy resin.
The proper cure performance of any epoxy resin system is highly dependent on the quality and thoroughness of the mixture.
The resin and curing agent must be mixed to a homogeneous consistency.
Poorly mixed resin and curing agent yields tacky or uncured spots to appear.
Use these theoretical factors to determine coverage to unfilled epoxy resin as a theoretical guide.
It is also important to consider the type of substrate to be coated.
Soft wood like pine absorbs more resin.
Hard and dense wood species require less resin application.
Gallon To Volume Conversion1 Gallon = 231 CUBIC INCHES 1 Gallon = 128 OUNCES 1 Gallon = 3.7854 LITERS 1 Gallon = 4 QUARTS 1 Gallon = 16 CUPS |
Gallon To Weight Conversion 1 Gallon Of Mixed Epoxy Resin = 9.23 Pounds 1 Gallon Of Mixed Epoxy Resin = 4195 Grams |
To Calculate The Resin Coverage On A Flat Smooth Surface,
Determine The Length X Width X Thickness In Inches
To Obtain The Cubic Volume Inch Of The Mixed Resin Needed.
Use The Following Equation:
(Length X Width X Applied Thickness)/ 231 Cubic Inches Per Gallon = Cubic-inches Of Coating Needed
Example
50 Inches X 36 Inches X 0.010 (10 Mils) = 18 Cubic Inches
Visit Our Coating Coverage Calculator
Cut And Paste Following Link
http://instacalc.com/35245/embed
STORAGE
MAX GPE A/B should be stored in a cool dry place. Do not store above 30ºC for a prolonged period.
MAX GPE A/B has a 12-month shelf from the date of shipment when stored properly. Replace the caps tightly to prevent moisture contamination.
When properly stored this kit will last greater than 2 or more years.
RESIN CRYSTALLIZATION FROM PROLONGED STORAGE OR COLD WEATHER EXPOSURE
The resin component or the PART A may crystallize due to cold temperature exposure.
Please inspect the resin component for any solidified crystals which will appear as waxy solid or cloudiness on the bottom of the PART A bottle.
View the following video for identification and processing.
Do Not Use Unless Processed To Revert Any Crystallized Resin Back To A Liquid State And Avoid Poor Cured Results.
MAX GPE A/B Works Well As A Fiberglass Impregnating Resin.
Please review the following information on how to create fiberglass composites.
COMPOSITE FABRICATING BASIC GUIDELINES
By definition, a fabricated COMPOSITE material is a manufactured collection of two or more ingredients or products intentionally combined to form a new homogeneous material
that is defined by its performance that should uniquely greater than the sum of its individual parts. This method is also defined as a SYNERGISTIC COMPOSITION.
COMPOSITE MATERIAL COMPOSITION
REINFORCING FABRIC & IMPREGNATING RESIN
'ENGINEERED PROCESS'
EQUALS
COMPOSITE LAMINATE WITH THE BEST WEIGHT TO STRENGTH PERFORMANCE
With respect to the raw materials selection -fabric and resin, the fabricating process and the and curing and test validation of composite part,
these aspects must be carefully considered and in the engineering phase of the composite.
TYPES OF FABRIC WEAVE STYLE AND SURFACE FINISHING
FOR RESIN TYPE COMPATIBILITY
Fabrics are generally considered ”balanced” if the breaking strength is within 15% warp to fill and are best in bias applications on lightweight structures.
“Unbalanced” fabrics are excellent when a greater load is required one direction and a lesser load in the perpendicular direction.
- Tow: The bundle of individual carbon filaments used to weave carbon fabric. 50k tow means there are 48-50,000 carbon filaments in the tow. Smaller tow i.e. 12k, 6k, 3k and 1k are obtained by dividing the 50k tow into smaller bundles.
- Thread Count: The number of threads (tow in carbon and yarn in Aramid) per inch. The first number will be the warp count and the second will be the fill count.
- Fill: The threads that run the width of the roll or bolt and perpendicular to the warp threads.
- Warp: The threads that run the length of the roll or bolt and perpendicular to the fill threads.
- Finish: The chemical treatment to fiberglass making it compatible with resin systems, therefore improving the bond between the fiber and the resin. Finishing fiberglass typically decreases the fiber strength by as much as 50%. Both Silane and Volan finishes are epoxy compatible. Historically, Volan has been considered a softer finish for a more pliable fabric, but recent advances have yielded some excellent soft Silane finishes.
- Thickness: Measured in fractions of an inch. The thicker the fabric the more resin required to fill the weave to obtain a surface-smooth finished part.
Weaves:
- Plain weave means the warp and fill threads cross alternately. This is the most common weave.
- 4 Harness (4 HS Satin or crowfoot) weave means the fill thread floats over three warp threads, then under one warp thread. This weave is more pliable than the plain weave, therefore conforms to complex curves more easily.
- 8 Harness (8 HS Satin) weave means the fill thread floats over seven warp threads, then under one warp thread. This weave is the most pliable of the standard fiberglass weaves.
- 2 x 2 Twill weave means the fill thread floats over two warp threads, then fewer than two warp threads. This weave is found most commonly in carbon fabrics and is more pliable than plain weave.
Most fabrics are stronger in the warp than the fill because higher tension is placed on the warp fiber keeping it straighter during the weaving process. Rare exceptions occur when a larger, therefore stronger thread is used in the fill direction than the warp direction.
PLAIN WEAVE Is a very simple weave pattern and the most common style. The warp and fill yarns are interlaced over and under each other in alternating fashion. Plain weave provides good stability, porosity and the least yarn slippage for a given yarn count. | 8 HARNESS SATIN WEAVE The eight-harness satin is similar to the four-harness satin except that one filling yarn floats over seven warp yarns and under one. This is a very pliable weave and is used for forming over curved surfaces. | 4 HARNESS SATIN WEAVE The four-harness satin weave is more pliable than the plain weave and is easier to conform to curved surfaces typical in reinforced plastics. In this weave pattern, there is a three by one interfacing where a filling yarn floats over three warp yarns and under one. | 2x2 TWILL WEAVE Twill weave is more pliable than the plain weave and has better drivability while maintaining more fabric stability than a four or eight harness satin weave. The weave pattern is characterized by a diagonal rib created by one warp yarn floating over at least two filling yarns. |
![]() | ![]() | ![]() | ![]() |
Satin Weave Type Conformity Unto Curved Shapes